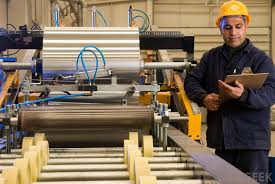
Nature of work
A quality engineer is in charge of monitoring the quality of a company's products or services for their customers. This entails discovering different ways to lower production costs and finding different ways to improve the quality of a product. He/she decides what metrics will be checked and in what manner and then conducts tests and applies statistical process control (SPC) tools and methods to identify improper quality control practices and examines quality systems for deficiencies. He/she collaborates with a design engineer to assess the critical characteristics of the product that will be measured. He/she constantly works on implementing improvements to enhance quality systems and develop training to improve the awareness of quality control issues. He/she analyzes defects and takes action to address customer complaints. Another typical duty is to compare the product to the original specifications. He/she also has to report any product irregularities to the person in charge. Additional duties include developing the different standards and methods for testing, measuring, and analyzing the products or services. He/she is also responsible for the documentation of the quality control in a company. Environment of work
Working hours and conditions vary between sectors, but sometimes long working hours might be required Weekend, shift work and on-call work is usually required in manufacturing where production is 24 hours a day. Work may be office based as in customer service operations, or factory based as in manufacturing process. Once experience has been gained, self-employment and freelance work are possible by working as a consultant to small firms or trainers. Career breaks are possible, but quality assurance techniques change and develop rapidly so it is important to keep up to date. Quality management is practiced in all industries in the public and private sectors and by firms and organizations of all sizes. Travel within a working day depends on the employer and may sometimes be frequent. Absence from home overnight or travel may be required; for example, for visiting customers, meeting to discuss quality plans or investigating particular quality issues. Professional life
Quality engineer is able to progress while remaining within the position of quality managing, which is becoming increasingly prestigious and central to organizations' activities. Working in quality assurance (QA) can also lead to management jobs in other areas of the business, such as production, health and safety and sales, and in areas such as human resources and customer services. His/her level of work may depend on the size and type of the organization. In large organizations, he/she may have more opportunities to specialize in a particular process area and to advance through the corporate structure. In small organizations, there may be the possibility to practice quality assurance in several different roles across the business, to feel closer to the front line of business activity, and to see the direct commercial impact of his/her contribution.Range of typical starting salaries: 50000 SYP.
Getting the job
Although this area of work is open to all graduates, the following subjects may increase his/her chances in the relevant fields:Physical / mathematical / applied science; engineering; business/management; textile technology; polymer science/technology.
A pre-entry postgraduate experience is not necessary, but a number of postgraduate courses are available and may improve his/her chance of entry. Many quality engineers gain skills from getting certified in Total Quality Management. These techniques improve his/her company’s processes and procedures while eliminating any defects in the products.
Skills
There are many skills she/he needs to have and tries to improve, such as:Dexterity, he/she should be able to quickly remove defected sample parts or products during the manufacturing process.
Math skills. Knowledge of basic math and computer skills are important because measuring, calibrating, and calculating is a major part of quality control testing.
Mechanical skills, he/she must be able to use specialized tools and machinery when testing products.
Stamina, he/she must be able to stand for long periods during work.
Technical skills, he/she must understand blueprints, technical documents, and manuals, ensuring that products and parts fully meet quality standards.
Sources and references
If you need any further information on what is included in this file, you can visit the following websites:- asq.org, American Society for Quality
- asq.org/pub/qe, Quality Engineering is a peer-reviewed, quarterly journal
- The Order of Syrian engineers, Damascus, Tel: 6627256
- www.arab-eng.org, Arab Engineers Forum.
- Arab Standard Classification of Occupations, 2008, Ed. Arab Labor Organization.